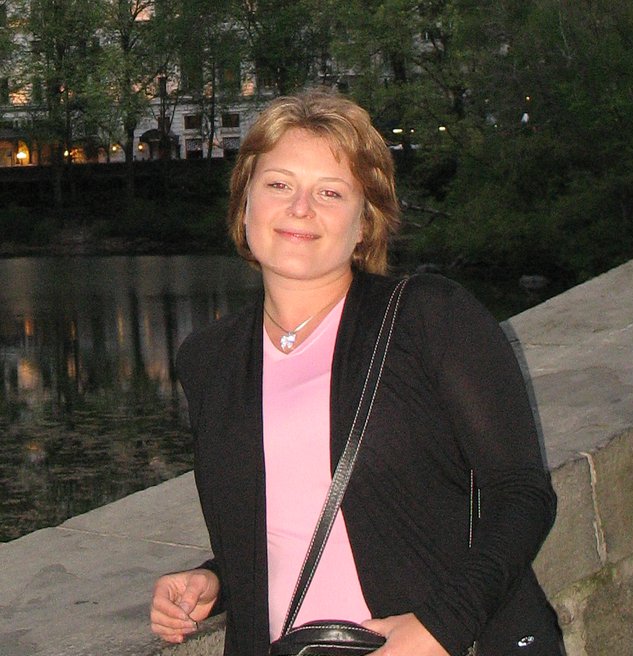
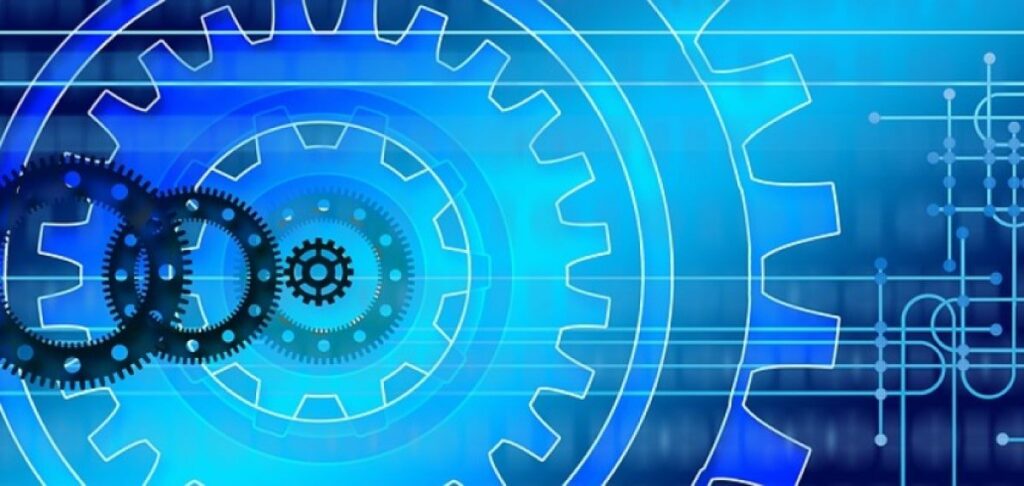
Basic Principles of the Systems Approach
In the systems approach, every organization is considered an open system that can change under the influence of internal and external factors. It is always distinguished from other systems by the presence of a goal, such as profit. All processes taking place in the company should be subordinated to this goal.
The system consists of interconnected elements (departments, divisions, branches). They may have their own tasks, but they do not conflict with other elements and the common goal. Each of them contributes to the formation of the system’s unity, and elements that are of secondary importance in one environment may become important when circumstances change.
Carl Ludwig von Bertalanffy developed the systems approach
The main task of system management is to identify and improve the mechanisms linking all its elements, to make them move towards a common goal. To do this, it is necessary to be able to move from unity to decomposition and back again. That is, to evaluate the system as a single whole, to break it down into its component parts, to put their connections in order and again to evaluate the system as a single organism.
Triad “input – transformation – output”
An open system always has an “input” (everything that comes from outside: information, capital, human resources, materials, equipment, etc.) and an “output” (volume of goods and services).
Inside the system, due to its “energy” (people, tools, innovations) there is a process of “transformation” of input components into output components. With the help of the triad “input – transformation – output” we can describe the dynamics of any system. Its analysis begins with the study of “output” parameters, which gives an understanding of what goods and services should be produced, in what time frame, at what price to get competitive products (services) and understand who will be its buyer.
After that, the “input” parameters are determined, i.e. analyze the need for resources and study the processes that transform them into finished products. The more efficient this transformation is, the more added value the “outputs” of the system have and the greater their number.
Advantages of the system approach
Many companies follow the path of local optimization, when each middle manager strives to improve the performance of his or her department as much as possible. However, he often fails to take into account that if he succeeds, his actions will harm the organization as a whole. For example, from the point of view of the head of the transportation department of a distribution company, it makes no sense to deliver goods more than once a week, because the car will drive half-empty. But if he makes such “optimization”, the company will lose a lot of customers who want to receive the goods more often. With a systematic approach, this will not happen, because the solution of private problems is always subordinated to the achievement of the main goal.
The systemic approach does not focus on individual elements, but looks at the organization as a whole.
In addition, a systematic approach minimizes the role of the individual in the success of the company. Organizations where everything is tied to the manager (his connections, professionalism, personal qualities, management style, etc.) tend to be very unstable. If he gets sick for a while or, even worse, quits, the work process falls apart before your eyes.
With a systematic approach, any production process in the company is brought to automaticity, so daily activities go “by themselves”, without direct intervention of the manager, whose efforts are instead directed to innovation and planning.
The process of personnel training is also facilitated. In fact, the task of a newcomer is reduced to the fact that, having familiarized himself with the job descriptions, he “fits” into the system. Thanks to the competent organization of all processes in the company, the system will take care of his further training and prevent him from making serious mistakes.